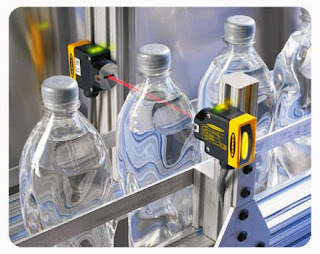
Un
sensor es un dispositivo capaz de detectar magnitudes físicas o químicas, llamadas variables de instrumentación, y transformarlas en variables eléctricas. Las variables de instrumentación pueden ser por ejemplo: temperatura, intensidad lumínica, distancia, aceleración, inclinación, desplazamiento, presión, fuerza, torsión, humedad, movimiento,
pH, etc. Una magnitud eléctrica puede ser una resistencia eléctrica (como en una RTD), una capacidad eléctrica (como en un sensor de humedad), una tensión eléctrica (como en un termopar), una corriente eléctrica (como en un fototransistor), etc.
Un sensor se diferencia de un transductor en que el sensor está siempre en contacto con la variable de instrumentación con lo que puede decirse también que es un dispositivo que aprovecha una de sus propiedades con el fin de adaptar la señal que mide para que la pueda interpretar otro dispositivo. Como por ejemplo el termómetro de mercurio que aprovecha la propiedad que posee el mercurio de dilatarse o contraerse por la acción de la temperatura. Un sensor también puede decirse que es un dispositivo que convierte una forma de energía en otra.
Áreas de aplicación de los sensores: Industria automotriz, robótica, industria aeroespacial, medicina, industria de manufactura, etc.
Los sensores pueden estar conectados a un computador para obtener ventajas como son el acceso a una base de datos, la toma de valores desde el sensor, etc.
En esta oportunidad Expusimos el tema 5: Sensores Inductivos y Capacitivos.
Presentación del tema.